Recognizing the Basics and Applications of Plastic Extrusion in Modern Production
In the realm of contemporary production, the technique of plastic extrusion plays a crucial role. Unwinding the basics of this process reveals the real versatility and capacity of plastic extrusion.
The Principles of Plastic Extrusion Refine
While it might show up complex, the basics of the plastic extrusion process are based on reasonably simple concepts. It is a production procedure wherein plastic is thawed and afterwards formed into a constant profile with a die. The raw plastic product, usually in the type of pellets, is fed into an extruder. Inside the extruder, the plastic undergoes warmth and stress, creating it to thaw. The liquified plastic is after that required through a designed opening, recognized as a die, to create a long, continuous product. The extruded product is cooled down and after that cut to the wanted size. The plastic extrusion procedure is thoroughly utilized in different industries due to its effectiveness, versatility, and cost-effectiveness.
Different Kinds of Plastic Extrusion Techniques
Building upon the basic understanding of the plastic extrusion procedure, it is essential to check out the numerous techniques associated with this manufacturing approach. Both main techniques are profile extrusion and sheet extrusion. In profile extrusion, plastic is thawed and created into a constant account, commonly utilized to create pipelines, poles, rails, and window frames. On the other hand, sheet extrusion produces big, level sheets of plastic, which are normally more processed right into items such as food product packaging, shower drapes, and cars and truck components. Each technique requires specialized equipment and specific control over temperature and stress to make certain the plastic maintains its shape during cooling. Comprehending these strategies is key to utilizing plastic extrusion efficiently in modern manufacturing.
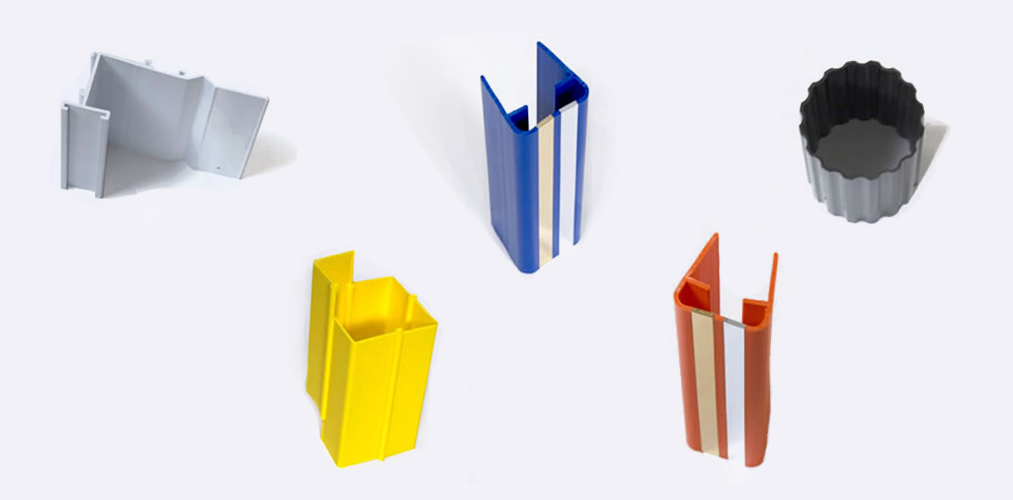
The Role of Plastic Extrusion in the Automotive Sector
An overwhelming bulk of parts in modern-day cars are products of the plastic extrusion process. Plastic extrusion is mainly used in the production of various auto components such as bumpers, grills, door panels, and control panel trim. Therefore, plastic extrusion plays a critical duty in vehicle production.

Applications of Plastic Extrusion in Consumer Goods Production
Beyond its considerable influence on the automobile industry, plastic extrusion proves similarly reliable in the world of consumer items manufacturing. The versatility of plastic extrusion permits manufacturers to create and generate complicated forms and dimensions with high accuracy and efficiency. The versatility, flexibility, and cost-effectiveness of plastic extrusion make it a preferred option for numerous consumer items manufacturers, contributing original site significantly to the market's growth and advancement.
Ecological Impact and Sustainability in Plastic Extrusion
The prevalent use of plastic extrusion in producing welcomes examination of its environmental ramifications. Reliable machinery reduces power use, while waste management systems recycle scrap plastic, lowering raw material demands. In spite of these enhancements, further advancement is needed to minimize the environmental impact of plastic extrusion.
Final thought
To conclude, plastic extrusion plays an important role in modern-day production, particularly in the automotive and customer products industries. Its adaptability enables the manufacturing of a large range of elements with high precision. Its potential for reusing and advancement of biodegradable materials uses a promising method towards lasting methods, therefore addressing ecological problems. Understanding the essentials of this procedure is essential to maximizing its applications and benefits.

The plastic extrusion process is thoroughly utilized in internet numerous sectors due to its cost-effectiveness, performance, and flexibility.
Building upon the basic understanding of the plastic extrusion procedure, it is essential to discover the different techniques entailed in this production method. plastic extrusion. In comparison, sheet extrusion produces big, level sheets of plastic, which are typically hop over to here more refined right into products such as food product packaging, shower curtains, and vehicle parts.An overwhelming bulk of components in modern-day lorries are products of the plastic extrusion procedure